Mould design
FI.DAL. Stampi boasts a technical department made up of highly experienced and trained personnel to guarantee the best design of moulds for plastics and die-casting.
Mould design is the first step, and one of the most important, in our work and is therefore the key to the optimal realisation of the finished product.
There are several factors to consider when designing a plastic mould and there are many questions that our technicians ask themselves before starting each project:
- What is the finished product for?
- Where will it be used?
- Does it have to mate with other parts?
- Will it be subjected to loads or pressures during its use?
These are just a few important questions to ensure an ideal design.
It is also essential to design according to the type of plastic material with which the part will be moulded, the thickness, size and complexity of the geometry.
In the design phase, for example, a careful study of how the plastic fills the mould cavities, the final part is cooled and the mechanisms act to release it determines the correct shape of the part required by the customer.
The way our engineers design is therefore the decisive basis for making a mould that must be easy to produce, easy to assemble, as durable as possible and as fast as possible in the subsequent plastic part moulding phase.
For highly complex moulds, in addition to the detailed study of the project, FI.DAL. Stampi is committed to providing customers with greater certainty by offering the possibility of using software to simulate the flow, cooling and deformation of plastic during the moulding process (Moldflow) and the creation of the prototype of the final part through the use of our 3D printer.
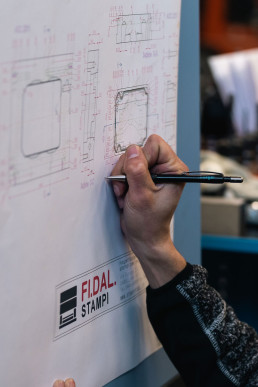